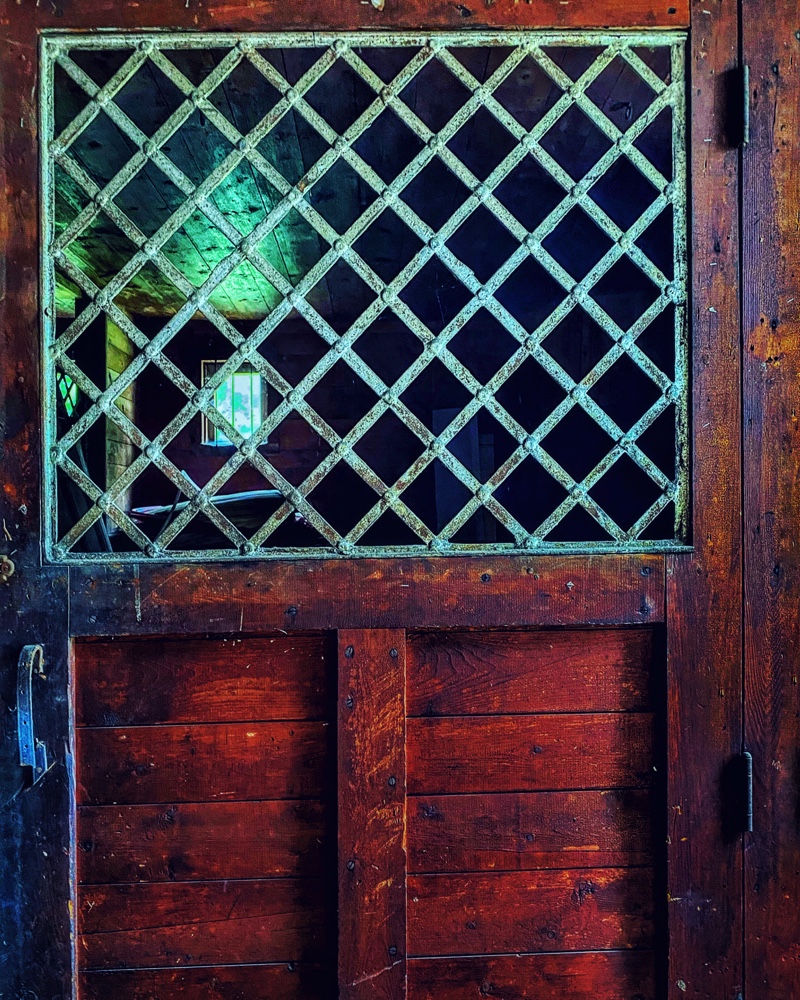
Horse Stall Haiku
Carriage house stall door,
pockmarked, patinated, but hale,
relates tenants past.— Geo Davis
Wabi-sabi Horse Stall
Patina. Rust. Wear-and-tear. The horse stall door in the photograph above abounds in visible reminders of imperfection and impermanence. And yet beauty brims. The image, indeed the horse stall and the horse stall door themselves, exude warmth and comfort and reassurance. No frisky filly within. No stately stallion. Yet life has invested this space with memories and, as Donna Baribeau pointed out, “Authentic Beauty”. The bumps and bruises of horses and those who tend them are part of this carriage barn story. But for much of the last 200+ years that Rosslyn has presided over Merchant Row there were no carriages and no horses in this barn. The stables were repurposed for storing firewood, bicycles, lawn mowers, lumber, tools, children’s forts, and possibly briefly even as a bedroom (if firsthand accounts are accurate.) All of this, and more, has left marks and stories. All of this contributes to the wabi-sabi allure of this space (and this photograph of the space.)
In traditional Japanese aesthetics, wabi-sabi (侘寂) is a world view centered on the acceptance of transience and imperfection. The aesthetic is sometimes described as one of appreciating beauty that is “imperfect, impermanent, and incomplete” in nature… Characteristics of wabi-sabi aesthetics and principles include asymmetry, roughness, simplicity, economy, austerity, modesty, intimacy, and the appreciation of both natural objects and the forces of nature. (Source: Wikipedia)
Wabi-sabi is at the root of my attraction to time-worn buildings and artifacts. I consider aging utility buildings — barns, boathouses, ice houses, sugarshacks, etc. — to be at least as intriguing as old houses. More sometimes. So many relics, unselfconscious, candid. Less penchant for concealing, fewer makeovers, more concurrently present years and lives. Sometimes it’s the old, banged up subjects and objects that look the best. Thank goodness for that!