I started an update a couple of weeks back that never made it out of the nest. An unfledged fledgling… At issue? Heat and humidity stabilization in the icehouse to properly acclimatize lumber pre-installation.
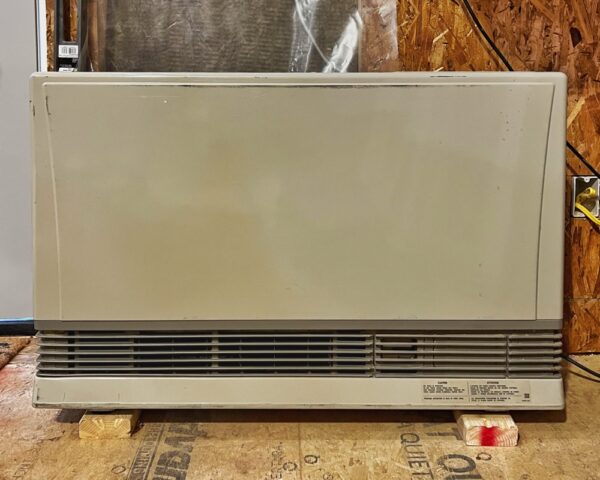
Given a few savvy questions about how we planned to install finish woodwork (flooring, paneling, etc.) in the icehouse — which until recently still had no heat and still had leaky apertures where windows and doors won’t be installed until May — I had initiated a quick explanation for how we planned to temporarily stabilize the temperature and humidity to ensure predictable, effective lumber acclimatization. Initiated but then neglected. The questions have continued, mostly from carpenters a others savvy to the expansion and contraction of wood. So I’m returning to the topic, better late than never?!?! The silver lining? Our plan for stabilizing the heat and humidity was implemented a couple of weeks ago. And it’s working well.
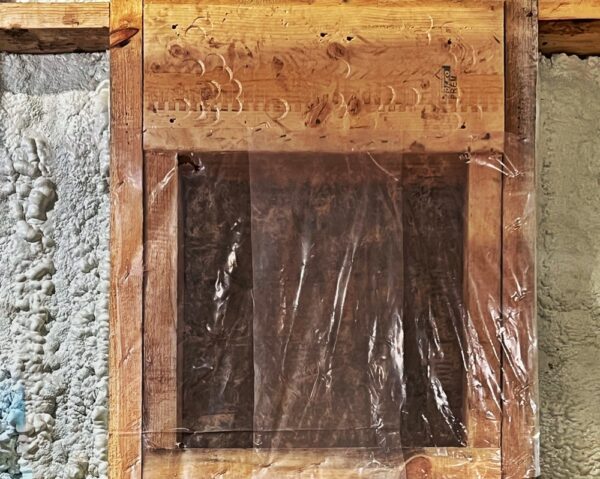
After my last visit Eric and Peter coordinated, source, installed efficient LP monitor heater that is thermostatically controlled and piped temporarily to an external propane tank. This setup, in conjunction with well insulated apertures, has effectively enabled us to stabilize the interior of workspace for the coming months, creating a heat and humidity controlled “envelope” where temperature and moisture are stable so that finish lumber can be properly acclimatized.
Another positive twist of fate: Eric was able to source an oversized monitor heater (more than satisfying our BTU needs for the small space) that had been previously but lightly used at a discounted price. Win, win. Hurrah, Eric!
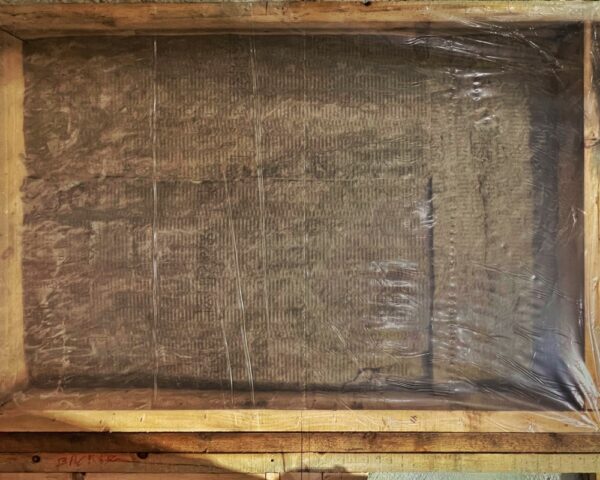
The photo at the top of this post is the monitor heater, and the next two photographs show examples of interior vapor/air barriers (plus rock wool insulation) that were added to the apertures. Window and door framing was undertaken prior to installation of the ZIP System paneling, so there was already a decent barrier in place for these apertures. But we needed to further improve thermal and moisture barriers, especially on the north and west elevations where ample fenestration made it more challenging to control the interior work environment 24×7.
With the monitor installed and working well and the interior/exterior barrier effectively controlled, there remained one additional temporary-but-important complement: a secure, functional access for day-to-day work. Ad-hoc closure systems had been adequate early on, but it was time to install a convenient but lockable, well insulated, pre-hung exterior door.
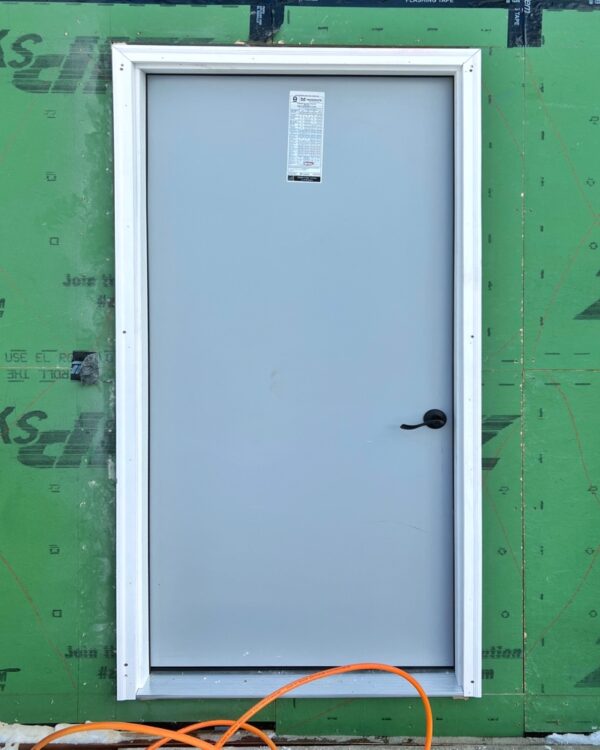
Kudos to Peter and Eric buttoning up the space to ensure forward progress over the last couple of weeks. I’m looking forward to witnessing firsthand tomorrow afternoon the hardwood flooring (beech) in the loft, for example, an accomplishment that was possible only once the heat and humidity stabilization was complete and the materials had acclimated on site for a couple of weeks.